The Situation
Located in Tomball, Texas, Houston Poly has been wrapping Innovation since 1979. They are a fully integrated, custom manufacturer of extruded polyethylene films, biodegradable and sustainable films, bags, shrink films, and flexible packaging. As a continuous process manufacturer with four production crews of 16+ personnel 24/7/365, lost time due to a power outage is lost revenue and additional labor costs.
Looking for a Solution
Wes Sumner, General Manager of Houston Poly, was concerned about the grid failure and facility shutdown during Uri, the severe winter storm in February 2021. With their energy broker’s help and Mr. Sumner’s analysis team, including the plant engineering team and his CFO, they began investigating solutions to keep the lights on no matter what the weather was doing.
According to Mr. Sumner, standby generation was a “no-brainer,” but there were many questions from the demand side. One of their first realizations is that ROI wouldn’t be the prominent driver. Mitigating risk, power resilience, and peace of mind would play significant roles in further exploring standby generation for the facility.
The municipality was contacted with what Houston Poly was interested in doing. Because the city’s team was new to this concept, they required Houston Poly to conduct a gas study and a comprehensive engineering report that delayed the process.
Once the city was satisfied, the Houston Poly’s team began researching vendors but wasn’t getting the required answers and service until they spoke with WPI. WPI was straightforward and understood what and why Houston Poly was searching for power resilience.
Is a continuous process manufacturer (CPM) a good fit for Demand Response?
Flexibility with tasks that require large amounts of electricity is the key. A manufacturing plant that can shift its scheduled tasks can save energy costs while sacrificing little to no productivity loss. For example, start-up processes generally have lower energy demand and can be planned for peak periods when electricity is higher.
The Solution
WPI’s proposal was accepted for seven Generac Standby Generators. The specifications and capabilities are as follows:
- 7 X 500kW 480 VAC Generac Natural Gas generators. These generators are Generac MPS units capable of self-parallel without to use of traditional paralleling switchgear. This feature allows Houston Poly to add generation in a “plug and play” fashion if future generation is required – Practical Power Resilience™.
- These seven units are capable of fully automatic operations, driving power to and from the generator plant. They start when required and self-parallel before feeding a 4000 Amp Automatic Transfer Switch (ATS). Once enough units are paralleled, the ATS transfers the building onto the generator plant.
- Comprehensive turnkey installation and commissioning.
Q & A with Wes Sumner
Q: What would be your advice to others considering standby generators?
A: “Put the time and effort into learning about what support is available and the OEM’s and distributor’s references and reputation.”
Q: Would you recommend WPI to a colleague?
A: “Absolutely! Industry knowledge and service before the sale blew away the competition.”
Q: What have your employees thought about the generators?
A: “The generatohrs have added to the employee’s morale, and confidence that the business is growing and stable – their jobs and paychecks are secure.”
For more information on Demand Response and Standby Generation, don’t hesitate to contact Daniel Barbersek, Director of Power Generation, Waukesha Pearce Industries.
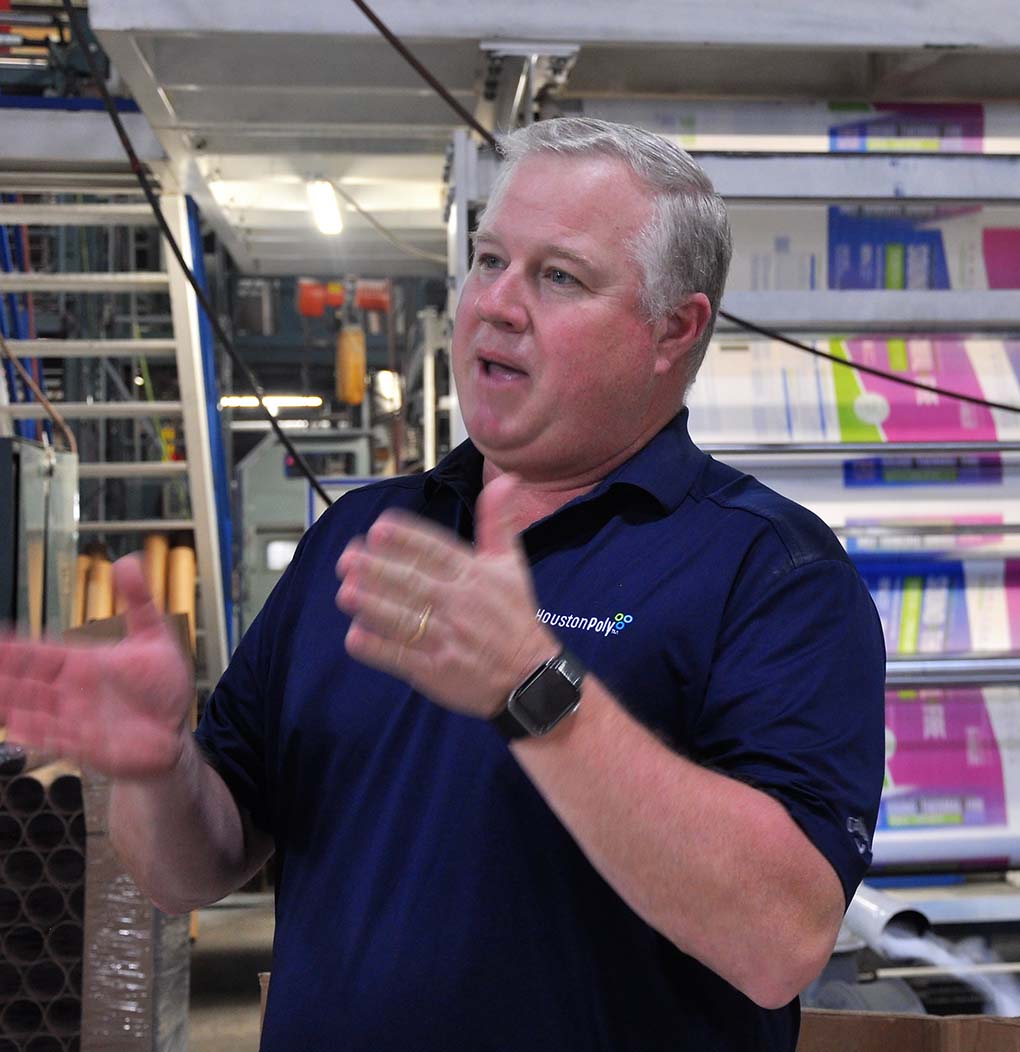
Wes Sumner
General Manager
Houston Poly